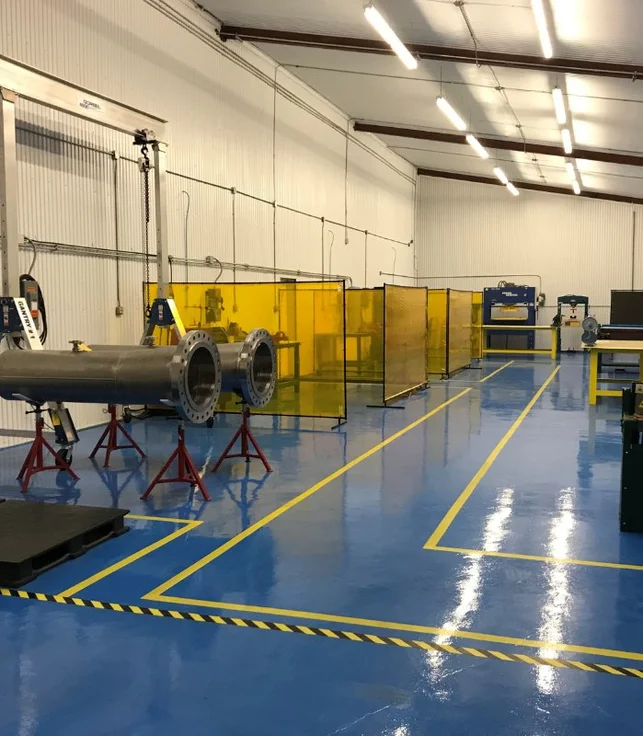
Anticorrosion Equipment Service Centers
Mersen Service Centers offer complete packages of services that optimize the life and performance of Corrosion Resistant Heat Transfer Equipment throughout their lifecycle.
From efficient preventive maintenance and inspection, to experienced repair and training, our goal is to keep your system operating at peak performance with minimum unplanned downtime.
-
Support
Keep your corrosion resistant equipment running at optimum performance
Mersen not only delivers equipment, but also provides support for all products throughout their life cycle. Standards are constantly changing, and technical improvements are being made all the time. That’s why it is crucial to have a partner with the product and process know-how to consult, diagnose, and make recommendations regarding the latest market requirements.
Our broad range of services include:
- Repair
- Spare Parts
- Preventive Maintenance
- Field Support
- Upgrades
- Training
- Emergency Response
-
Equipment repair
Our range of services
From efficient preventive maintenance and inspection, to experienced repair and training. Our goal is to keep your system operating at peak performance with minimum unplanned downtime.
Our goal is to keep your system operating at peak performance with minimum unplanned downtime.
Quality workmanship
Our technicians are highly experienced and skilled. Their ability to provide fast analysis and repair solutions can save your company time and money. Our centers are ASME compliant and we offer warranties for our work.
-
Our services and solutions
-
Repair
Complete repair services
We understand that interrupting production seriously impacts our customers’ business. That is why we are fully staffed with a team of experts to provide complete repair services, on site or in one of our service centers. Thanks to their extensive product knowledge, they are able to make a fast diagnosis and repair.
-
Maintenance
Preventive maintenance
Our experts will inspect and evaluate your system to determine the best preventive maintenance program for your plant. Preventive maintenance allows you to pre-plan the times your system will be down for service. In addition, costly failures are minimized and optimum performance is achieved.
-
Support
Field support
Mersen service specialists are available to consult, troubleshoot, commission, start-up, inspect, evaluate and provide options. Due to our years of experience and know-how, we can provide valuable insight for your specific system and process.
-
Start-up
Specific know-how
Start-up is a critical phase, and its success depends on many factors specific to each processing system. Our vast experience in graphite equipment means that we are able to help your company with a successful start-up.
-
Audit
Upgrades
Our team of process experts can audit your installation, identify areas where your existing equipment can be enhanced, and recommend upgrades to improve performance and extend life.
-
Training
Support and training
Our highly trained specialists can train your staff on routine maintenance and equipment repairs, as well as safety standards. Our team of system technicians are available to provide support and training onsite or at one of our service centers.
-
Spare parts
OEM parts
To keep Mersen equipment working optimally, OEM parts are required. Spare parts are manufactured to the highest level of precision and work flawlessly with our equipment. Mersen delivers spare parts around the world.
-
Emergency response
Quick action
Rapid response is critical when something goes wrong. With two strategically-located Service Centers, Mersen is able to provide quick action should an emergency occur.
-
-
Repair center
Graphite equipment repair center
Mersen Service Centers offer complete packages of services that optimize the life and performance of Corrosion Resistant Heat Transfer Equipment throughout their lifecycle.
Services offered
- Reengineering
- Reimpregnation
- Retubing
- Replacement of Parts
- Refurbishing
- Full Code Welding Capabilities
- Recertification with ASME Repair Stamp
- Repair of HCL Systems
- Full Service Machine Shop
- Field Assessment Services
- Preventive maintenance
- Field support
- Upgrades
- Training
- Spare Parts
-
Services centers
Locations
- 28,000 sq ft repair shop
- Certified Code Repair Facility
- ASME section VIII "U" stamp and NBIC compliant
Services:
- Graphite equipment repair
- Rebuild & service capabilities
- Code metal work
- 96,000 sq ft manufacturing facility
- 12,000 sq ft Ta/RME equipment manufacturing and repair building (6,000 sq ft climate controlled)
- Certified Code Repair Facility
- ASME compliant
Services:
- Full manufacturing capabilities
- Graphite equipment & synthesis unit repair
- Rebuild & service capabilities
- Code metal work
- Ta/RME equipment repair
- Field service
- 11,000 sq ft repair shop
- Certified Code Repair Facility
- ASME compliant
Services:
- Graphite equipment repair
- Rebuild & service capabilities
- Code metal work
-
Services centers
Management team
-
Drew Sholar
Service Center Manager/GM
Drew started in the graphite equipment industry as a technician at "Graphite Repairs" over 20 years ago. In 2010, when Mersen took over, he was promoted to the head of the Gonzales facility due to his expertise in service and repair.
Phone: (225) 647-6752
E-mail: drew.sholar@mersen.com
Expertise: Graphite and reactive metals equipment repair -
Tim Smith
Service Center Manager
Tim has more than 12 years of field service and manufacturing experience and joined Mersen as the Field Service Manager in 2019. He quickly grew his knowledge of Mersen's Anticorrosion Equipment portfolio via hands-on repairs and customer site services and was promoted to Salem Service Center Manager in 2021.
Phone: (540) 655-8055
E-mail: tim.smith@mersen.com
Expertise: Graphite, SIC, PTFE lined equipment repairs, technical support and troubleshooting, synthesis units, equipment and systems upgrades -
Keith Cummins
Service Center Manager/GM, LGI
Keith has more than 35 years in the graphite industry, specializing in maintenance, troubleshooting, and repairing of heat transfer equipment. Keith is a pioneer in the development of new repair technologies and unique solutions to difficult challenges.
Phone: (502) 893-6575
E-mail: sales.lgi@mersen.com
Expertise: Metal and graphite heat exchangers
-
-
Repair Center
TA/Reactive Metal Equipment
Formely AstroCosmos Metallurgical, Mersen has the technology, quality, and skills required to successfully repair reactive metals equipment. A staff with 70+ years of experience and expertise on Tantalum, Zirconium, Titanium, Niobium, and Nickle alloys Mersen can efficiently assess and execute event the most difficult of projects.
Mersen's service center and fabrication facility, strategically located in Salem, VA, provides a complete spectrum of production and repair capabilities.
With more than 96,000 square feet of combined fabrication and machining area, Mersen offers services on-site for planned maintenance or emergency outages.
- 96,000 sq ft repair shop
- 6,000 sq ft dedicated climate-controlled Ta/RME area
- Certified Code Repair Facility
- ASME section VIII "U" stamp and NBIC compliant
- Inventory of Ta, Zr and Ti Tubing and Sheet & Plate to support repair work
-
On-site and field services
Salem, Virginia
Services offered:
- Visual inspections, testing, reporting of findings
- Reactive Metal equipment welding and fabrication
- Reactive Metal piping welding
- Repair of solid, lined, cladded RME equipment
- Retubing and repair of RME heat exchangers
- Repairs of other RME components and parts such as piping spools, injection nozzles, lined heads, lined plates
- Hydro, air/soap, helium leak testing, dye penetrant inspection
- Machining
- Heat treat oven
- Engineering calculations, drawings & design expertise
Field Services:
- Fit and weld RME piping spools and assemblies
- Assessments
- Repairs – vessels, columns, heat exchangers, agitators
- Alterations
Materials:
- Tantalum
- Zirconium
- Titanium including Ti-Palladium
- Duplex Stainless Steel
- Nickel Alloys
-
Salem, Virginia
Management team
-
Jonathan Branch
Ta/RME Shop Manager
Jon started with AstroCosmos Metallurgical in 2008 as a Quality Control Inspector and became a Supervisor in 2011. In 2014 Jon transferred to the Louisiana fabrication facility and was promoted to Quality Assurance Manager. Jon has 21 years of experience in metal fabrication; 16 of those years have been in inspection and 11 years exclusively with reactive/refractory alloys. Jon is extremely knowledgeable with ASME, NBIC, TEMA, PED and SQL code requirements. In 2020, Jon relocated to the Salem facility as part of his promotion to Ta/RME production manager.
Phone: (540) 378-0358
E-mail: jonathan.branch@mersen.com
Expertise:Fabrication and inspection of reactive metal and graphite chemical process equipment, AWS Certified Welding Inspector, Level II RT, MT, PT, GPR technician -
David Frey
RME Technology Manager
David was employed by “AstroCosmos Metallurgical” from 1991 to 2017. He served in various positions including Quality Manager, Engineering Manager, Director of Project Management, VP Technology and Business Manager. David has extensive experience in reactive metal equipment design, fabrication, inspection and testing. David is an ASTM B10.0.3 Subcommittee Chairman (Ta & Nb) and an NACE TEG120x Reactive Metal Task Group Officer.
Phone: 805 402 5710
E-mail: david.frey@mersen.com
Expertise: Tantalum, zirconium and titanium metals, welding metallurgy and explosive clad fabrication of these metals
-
-
Anticorrosion Equipment Sales Network
Find below our contacts for sales information and quotation.
-
Contact us
Need to get information on our Services Centers