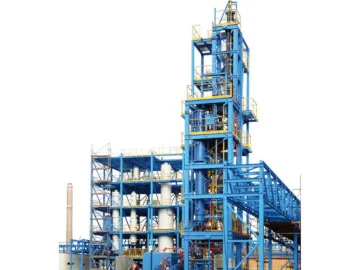
Revolutionizing chemical industry operations with graphite anticorrosion equipment
In the rapidly evolving chemical industry, Mersen stands at the forefront, revolutionizing operations with cutting-edge graphite anticorrosion equipment. Mersen's solutions are not just about enduring harsh environments; they're about leading the industry towards more efficient, safer, and sustainable chemical processing.
-
Using graphite anticorrosion equipment to redefine the chemical industry
The chemical industry, known for its rigorous and often corrosive environments, demands reliable and robust solutions for its operations. Graphite anticorrosion equipment emerges as a cornerstone in this sector, addressing various challenges and playing a pivotal role in ensuring process integrity and efficiency. Graphite, with its exceptional resistance to a wide range of chemicals, including acids and alkalis, is an ideal material for manufacturing equipment used in chemical processes. This includes columns and heat exchangers, which are subject to harsh conditions and corrosive substances. The durability and thermal stability of graphite anticorrosion equipment not only enhance the safety and lifespan of chemical processing systems but also contribute to the optimization of processes by minimizing downtime and maintenance costs.
-
Reducing downtime due to corrosion-related issues
I've witnessed firsthand the transformative impact of Mersen's graphite anticorrosion equipment on our operations. Their equipment has not only enhanced our process efficiency but also significantly reduced downtime due to corrosion-related issuesJami Blake
Production Manager
-
What is Graphite Anticorrosion Equipment?
Graphite anticorrosion equipment is an essential component in the chemical industry, known for its unparalleled resistance to corrosive environments. Crafted from graphite, a robust form of carbon, this equipment is highly resistant to a variety of corrosive materials, including strong acids and alkalis. Its applications are diverse, ranging from graphite blocks and tubes to graphite heat exchangers, all crucial in processing aggressive substances. The choice of graphite is due to its excellent properties: it not only resists corrosion but also withstands high temperatures and efficiently conducts heat. Graphite anticorrosion equipment is a cornerstone in the chemical industry, safeguarding the processes from the damaging effects of corrosive agents while enhancing operational efficiency and safety. This equipment is a testament to the advancements in industrial material science, offering durability, reliability, and performance in challenging industrial environments.
-
Graphite anticorrosion equipment
Need to get information on graphite anticorrosion equipment for chemical industry?
-
What are the benefits of Graphite Anticorrosion Equipment for chemical Industry?
Graphite anticorrosion equipment offers a myriad of benefits for the chemical industry, catering to the demanding needs of various processes.
Chemical resistance of the graphite anticorrosion equipment
Graphite's exceptional resistance to a wide spectrum of chemicals, including harsh acids and alkalis, makes it an ideal material for anticorrosion equipment. This resistance is vital in the chemical industry, where equipment frequently encounters corrosive substances. The use of graphite in equipment like graphite heat exchangers ensures the longevity of these systems while maintaining the purity of the chemical processes.
Thermal resistance of the graphite anticorrosion equipment
The high thermal resistance of graphite is crucial for applications involving extreme temperatures. In the chemical industry, where processes often involve significant heating or cooling, graphite equipment, composed of graphite tubes or graphite blocks, withstands these temperature variations without degradation, ensuring uninterrupted operations and safeguarding against equipment failure due to thermal stress.
Durability of the graphite anticorrosion equipment
In the demanding conditions of the chemical industry, the durability of graphite anticorrosion equipment is a significant benefit. This durability leads to reduced maintenance, longer equipment lifespan, and overall cost-effectiveness.
Heat transfer efficiency of the graphite anticorrosion equipment
Graphite's excellent thermal conductivity is key for efficient heat transfer in processes like those involving graphite heat exchangers. This property ensures optimal temperature control and enhances the efficiency and speed of chemical reactions.
Versatility of the graphite anticorrosion equipment
Graphite's versatility allows for a range of applications. Its ability to be machined into various shapes, such as graphite blocks and tubes, enables tailored solutions for specific chemical processes, accommodating diverse pressure and temperature conditions and unique system configurations.
-
What applications can graphite anticorrosion equipment be used for?
The versatility of graphite anticorrosion equipment makes it integral to various applications in the chemical industry, each with unique challenges and requirements.
Acid and Chlor-Alkali production
Graphite's resistance to a wide array of acids positions it as an essential material for equipment in sulfuric, hydrochloric, phosphoric, and hydrofluoric acid production. Its non-reactive nature is also crucial in the chlor-alkali industry, where exposure to chlorine and other corrosive chemicals is common. This resistance ensures the longevity and reliability of the equipment in these harsh environments.
Chemical Synthesis
The chemical industry relies heavily on graphite heat exchangers for the synthesis of numerous organic and inorganic compounds. The ability of graphite to withstand corrosive reactants and products without degrading is invaluable. It ensures the integrity and efficiency of processes, making graphite an indispensable component in chemical synthesis operations.
Distillation Processes
Graphite is extensively used in distillation processes due to its high thermal resistance and chemical inertness. Components like graphite internals, columns, and heat exchangers are widely employed, providing reliable performance in separating complex mixtures under various thermal and chemical conditions.
Electronic Chemicals
In the production of high-purity electronic chemicals, the non-contaminating characteristics of silicon carbide heat exchangers are vital. This material is chosen to prevent any impurities from compromising the quality of sensitive electronic products. Their anticorrosive properties are essential in maintaining the purity and quality of electronic chemicals. The graphite heat exchangers are used to recover the acid used in the process of high-purity electronic chemicals.
-
Graphite anticorrosion equipment
Need to get information on graphite anticorrosion equipment for chemical industry?
-
Mersen range of graphite anticorrosion equipment for chemical industry
-
Graphite blocks heat exchangers
Heat exchange
These heat exchangers are composed of graphite blocks with drilled holes for process and service fluids. Their design ensures maximum heat transfer while maintaining resistance to corrosion and thermal shock. Ideal for processes involving acidic or basic solutions, they are highly efficient in energy recovery, heating, or cooling operations.
-
Graphite shell and tube heat exchangers
Heat exchange
Marrying durability with efficiency, these heat exchangers consist of a shell (typically steel) containing a bundle of graphite tubes through which the process fluid flows. They are particularly suitable for handling large volumes of corrosive liquids at high temperatures, providing optimal heat transfer with minimal risk of corrosion.
-
Graphite plate heat exchangers
Heat exchange
These exchangers leverage the compact, efficient design of plate exchangers with the corrosion resistance of graphite. They offer high heat transfer coefficients, making them excellent for rapid heating or cooling of corrosive fluids, especially where space and energy efficiency are critical.
-
Graphite Annular Groove heat exchangers
Heat exchange
The annular groove design enhances the surface area for heat transfer, providing high efficiency in a compact form. This makes them suitable for applications requiring efficient temperature control of corrosive media, such as in reactive or absorptive processes.
-
Graphite HCl burner
Synthesis of hydrochloric acid
Designed for the synthesis of hydrochloric acid, graphite HCI burners resist the highly corrosive nature of HCl. They ensure consistent and safe operation in HCl production, with designs that minimize the risk of corrosion and enhance the efficiency of acid production.
-
Graphite bursting discs
Overpressure protection
Used as a safety mechanism, these discs provide overpressure protection in chemical processing equipment. They rupture at predetermined pressures, thus preventing potential damage due to overpressure scenarios in systems handling corrosive materials.
-
Graphite steam ejector vacuum group
Drying and distillation
These systems are used to create vacuum conditions essential in various chemical processes like drying and distillation. The use of graphite ensures they can operate reliably in corrosive environments, providing a consistent vacuum without contamination of the process.
-
Graphite columns and internals
Graphite columns and internals
Graphite columns and their internals, including packing and trays, are used in distillation, absorption, and stripping operations. Their corrosion-resistant properties make them suitable for processing a wide range of corrosive fluids, ensuring longevity and efficiency in continuous and batch operations.
-
-
How to choose your graphite anticorrosion equipment for chemical industry?
Selecting the right graphite anticorrosion equipment is crucial for ensuring efficiency, safety, and longevity in the chemical industry. Here are key factors to consider.
Assessing Chemical Compatibility
To ensure the longevity and effectiveness of your graphite anticorrosion equipment, it's vital to assess its compatibility with the chemicals used in your processes. Graphite is particularly suited for handling a range of corrosive substances. Verify the material's resistance to the specific corrosive agents in your operations to guarantee long-term reliability.
Evaluating Operational Conditions
Understanding the operational environment is crucial. This includes assessing the temperature and pressure ranges the equipment will face. Graphite materials, known for their corrosion resistance, are ideal for environments with extreme conditions, much like those found in processes using graphite heat exchangers or HCl burners.
Reviewing Equipment Design
When choosing equipment, consider the ease of maintenance and cleaning. Designs should adhere to international standards for safety and efficiency, as ASME, AD 2000 or PED. For example, when selecting graphite heat exchangers, ensure the design facilitates efficient heat transfer. This is particularly important for applications involving silicon carbide heat exchangers, where design intricacies can significantly impact performance.
Consider Customization Options
Lastly, explore whether there are customization options available. This could include tailored solutions for specific applications, such as custom-engineered graphite blocks or tubes to fit unique operational needs. The flexibility to adapt to evolving processes in the chemical industry is crucial for ensuring that your investment remains beneficial in the long run.
-
Why choose Mersen for your graphite anticorrosion equipment?
Mersen stands out as a leading provider of graphite anticorrosion equipment, especially for the chemical industry. Their expertise and capabilities make them an ideal choice.
Proven expertise
Mersen's longstanding history in the industry showcases their deep understanding and expertise in anticorrosion technology. With extensive experience in providing solutions for complex chemical processes, they are adept at handling the demands of the chemical industry, ensuring that equipment like graphite heat exchangers and HCl burners meet the highest standards.
Advanced material technology
Mersen is at the forefront of material technology, utilizing advanced materials such as graphite, silicon carbide, and PTFE in their equipment. This ensures superior performance in corrosive environments, making their products like graphite tubes, PTFE piping, and silicon carbide heat exchangers highly reliable and efficient.
Custom Engineering Solutions
Understanding the unique needs of each operation, Mersen offers custom-engineered solutions. Their capability to design and manufacture tailor-made equipment, such as graphite blocks and PTFE lined columns, allows for optimal performance tailored to specific process requirements in the chemical industry.
International footprint allowing local support
Mersen's global presence ensures they can provide local support no matter where your operation is located. This international footprint not only facilitates easier access to their products and services, including on-site maintenance and spare parts delivery, but also allows for a better understanding of regional requirements and regulations. This local support is crucial for industries that operate globally, ensuring consistent quality and service standards worldwide.
-
Questions about anticorrosion equipment for chemical industry
-
Does Mersen offer maintenance for graphite anticorrosion equipment?
Yes, we provide comprehensive maintenance services for our graphite anticorrosion equipment. This includes on-site maintenance, ensuring that the equipment remains in top condition and operates efficiently. Our global network ensures prompt and effective service.
-
What are the benefits of PTFE for PTFE piping, PTFE bellows and PTFE lined columns?
PTFE, known for its excellent chemical resistance and thermal properties, is ideal for use in harsh chemical environments. In products like PTFE piping, bellows, and lined columns, it offers superior resistance to corrosive substances, ensuring longevity and reliability of the equipment in the chemical industry.
-
What is an efficient HCl synthesis unit?
An efficient HCl synthesis unit, such as those offered by Mersen, is designed for optimal production of hydrochloric acid. These units are tailored to maximize yield and efficiency, incorporating advanced materials like graphite HCI burner for durability and effective heat management.
-
What is the difference between graphite heat exchanger and silicon carbide heat exchanger?
The main difference lies in their material properties. Graphite heat exchangers offer excellent resistance to corrosion and are suitable for a wide range of chemical applications. Silicon carbide heat exchangers, on the other hand, provide enhanced strength and thermal conductivity, making them ideal for extremely corrosive and high-temperature environments.
-
Can an HCl burner produce energy?
An HCl burner primarily functions to produce hydrochloric acid by burning hydrogen and chlorine. While it is not designed for energy production, the process can be integrated into systems where heat recovery is possible, contributing to energy efficiency in the broader chemical processing system.
-
-
Contact
Need to get information on graphite anticorrosion equipment for chemical industry?